Offloading Structural Steel for Novelis
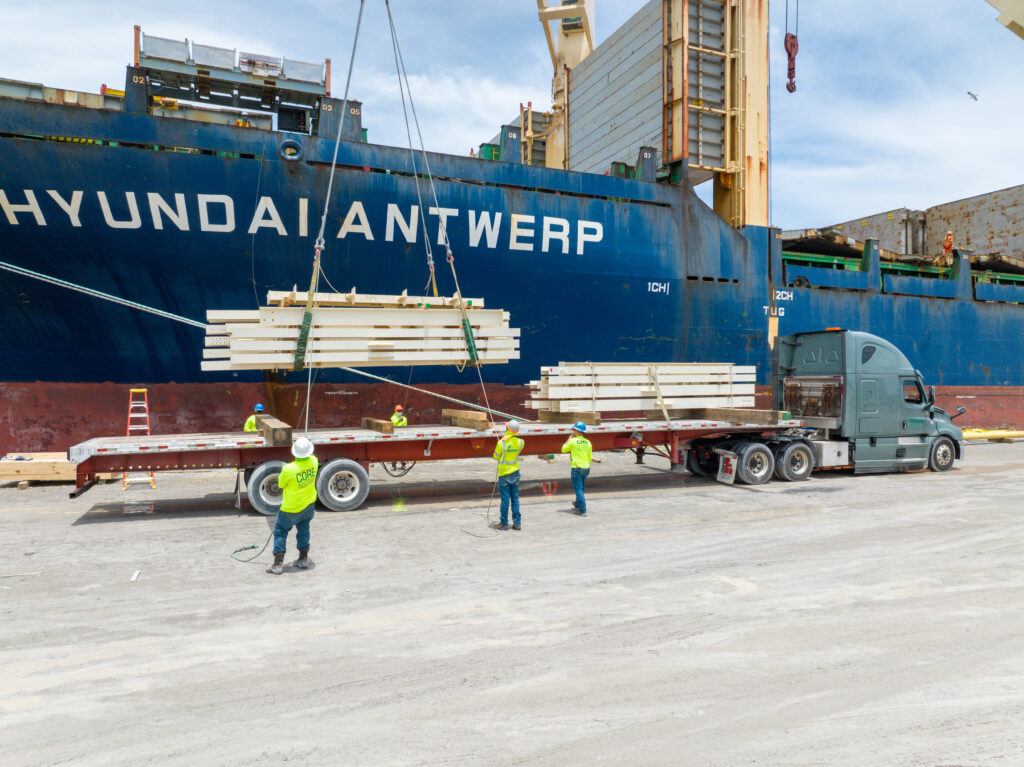
Core recently discharged 5,193 MT of structural steel from the M/V HYUNDAI ANTWERP for the Novelis plant in Bay Minette, Ala. Core’s 330-ton crane, forklifts, reach stackers and personnel were used. Horizon Freight Systems and Acme Truck Line Inc. transported the steel from dock to yard for storage.
Loading Stanchions
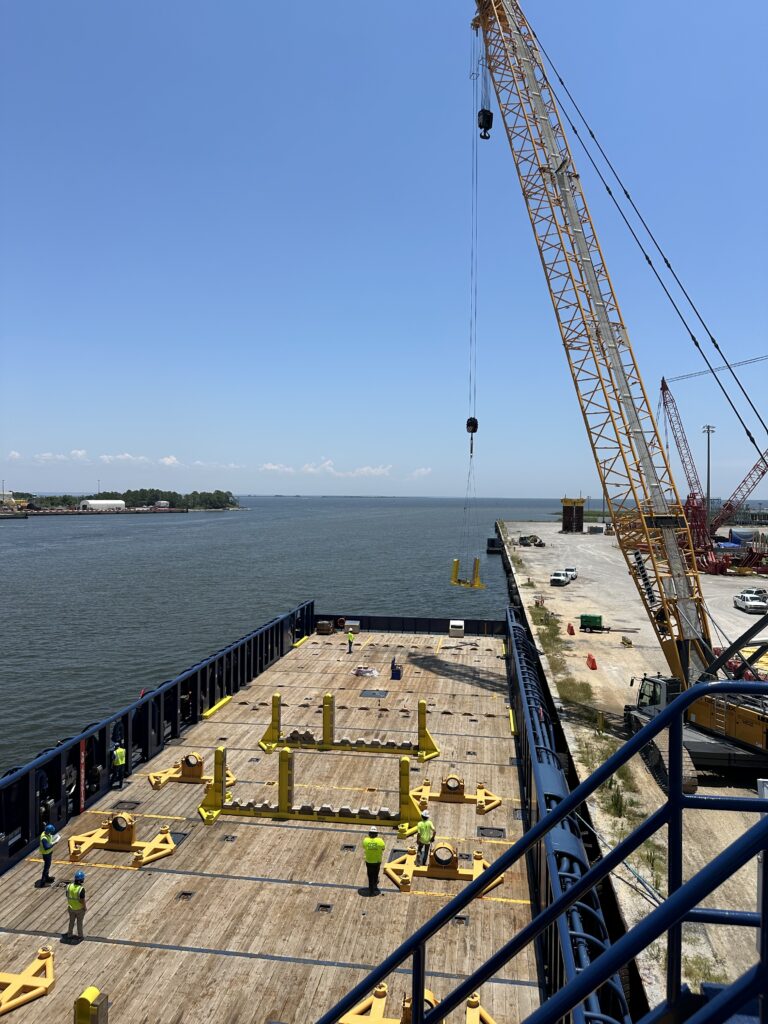
Core Industries recently loaded stanchions onto the OSV Harvey America and the OSV Harvey Energy. Both vessels departed the Core Dock to deliver the equipment to the Shell Perdido Platform in the Gulf of Mexico. Riser joints will be loaded onto the stanchions and returned to Core Industries for maintenance. The Perdido platform is the […]
Discharging Structural Steel
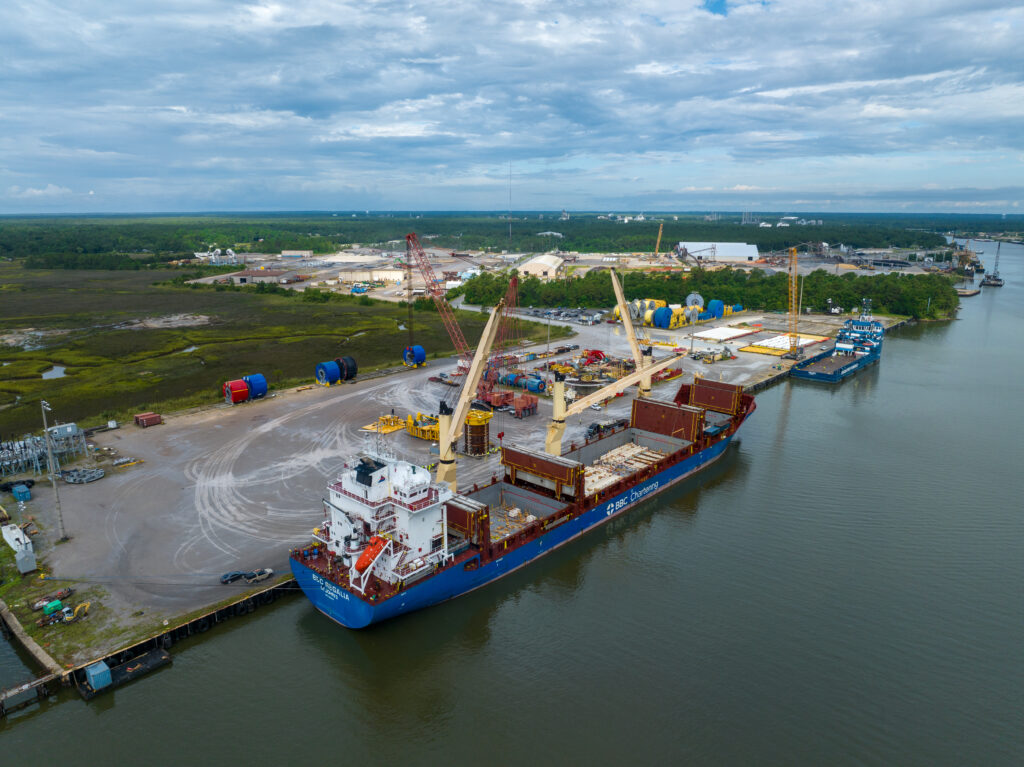
Core discharged 5,402 tons of structural steel from the M/V BBC REGALIA for the Novelis plant in Bay Minette, Ala. Core’s 330-ton crane, forklifts, reach stackers and personnel were used. Horizon Freight Systems transported the steel from dock to yard for storage. default default default
Discharging Aggregate
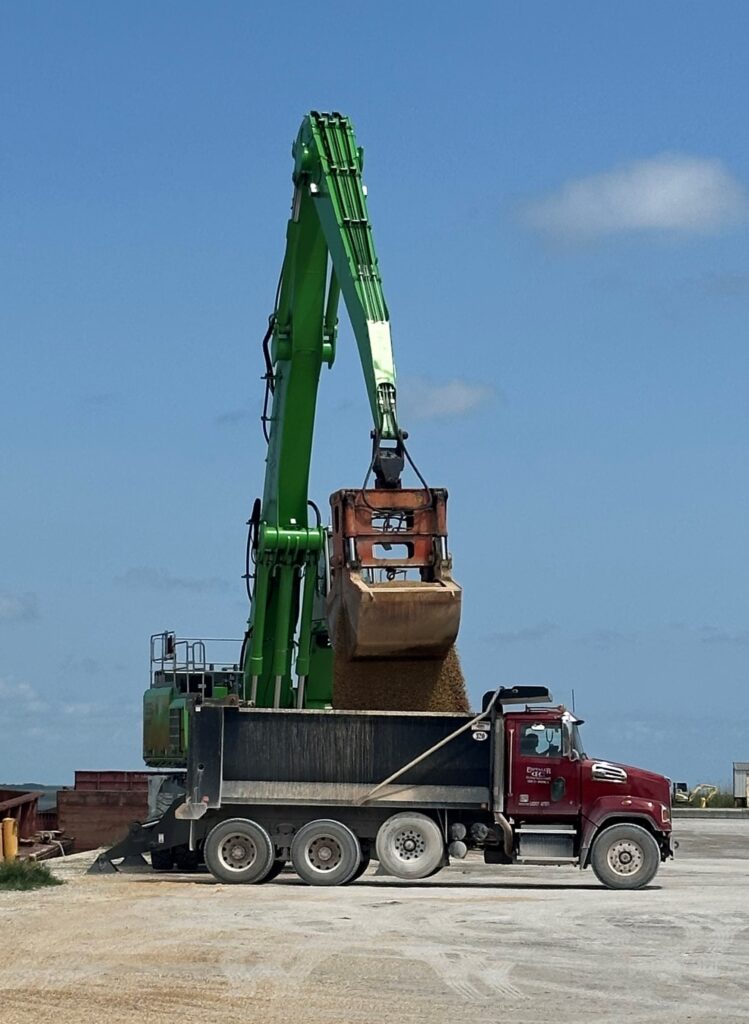
Core Industries recently discharged aggregate and concrete sand from barge for Couch Aggregates. Using its Sennebogen, Core unloaded 9,503 tons of aggregate and 3,085 tons of concrete sand to truck for transportation to storage pads. Core also used two front-end loaders and personnel to complete the job.
Discharging Structural Steel for Novelis
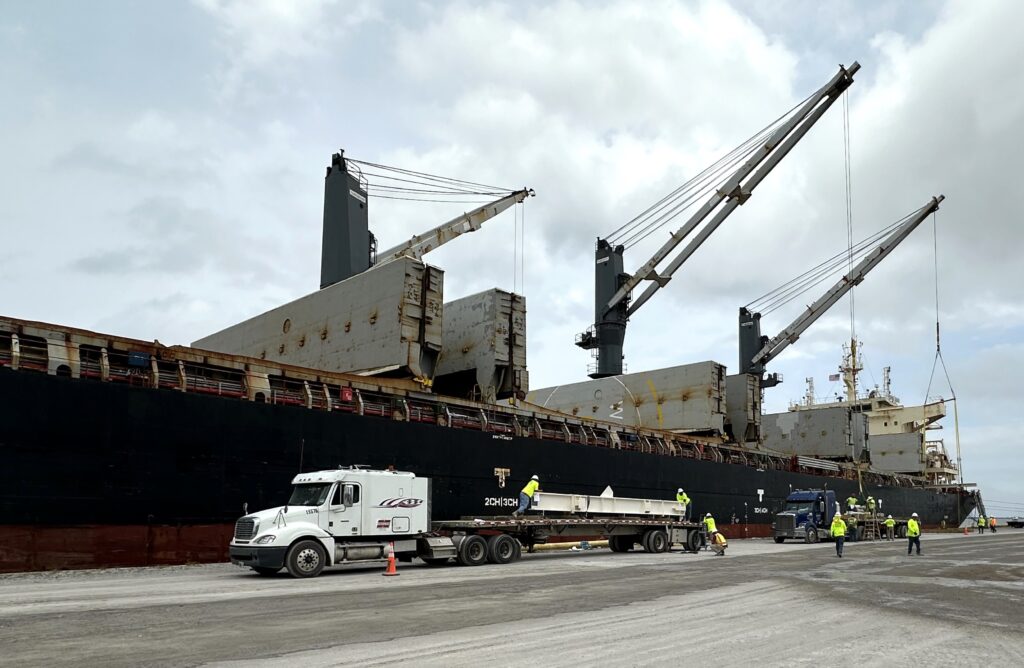
Core discharged 3,621 MT of structural steel from the M/V FRIEDERIKE SCHULTE for Novelis plant in Bay Minette, Ala. Core’s 330-ton crane, forklifts and reach stackers were used to complete the task. Horizon Freight Systems transported the steel from dock to storage.
Offloading Perlite
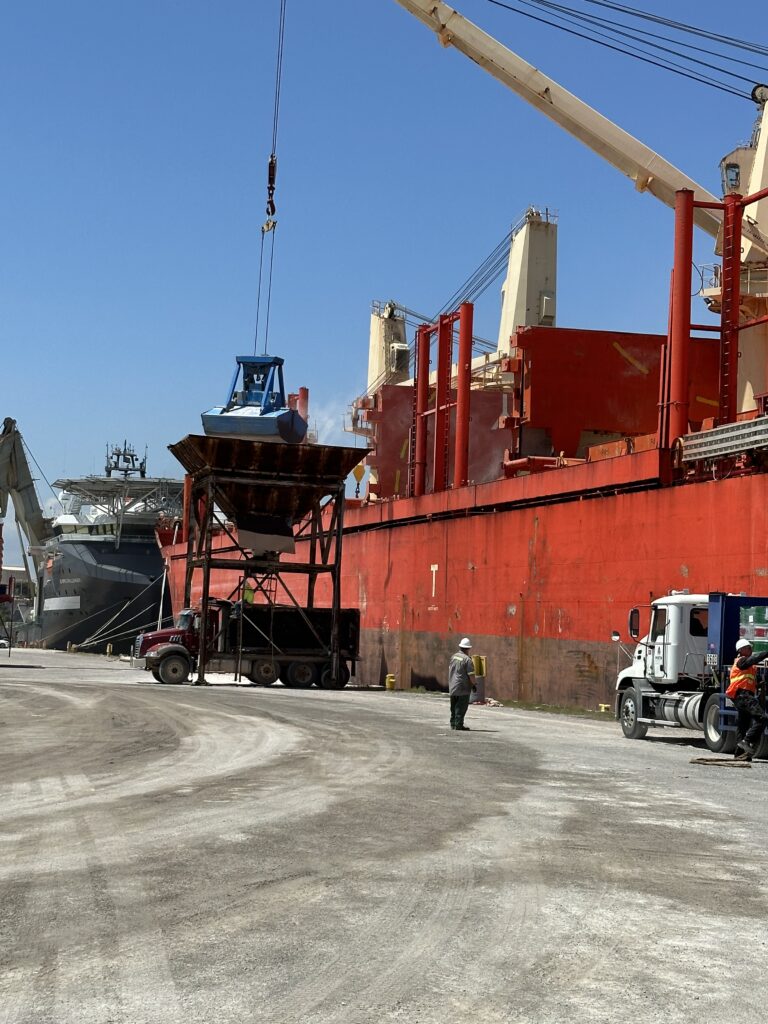
Core Industries recently offloaded 4,527 MT of perlite from the M/V KOTOR. Core used its clam shell buckets and two 644-ton loaders to complete the job for Imerys. Esfeller Construction transported the perlite from dock to Core’s warehouse for storage. Core Industries can handle all types of bulk material.
Loading Woodchips: M/V/ YILDIZLAR 3
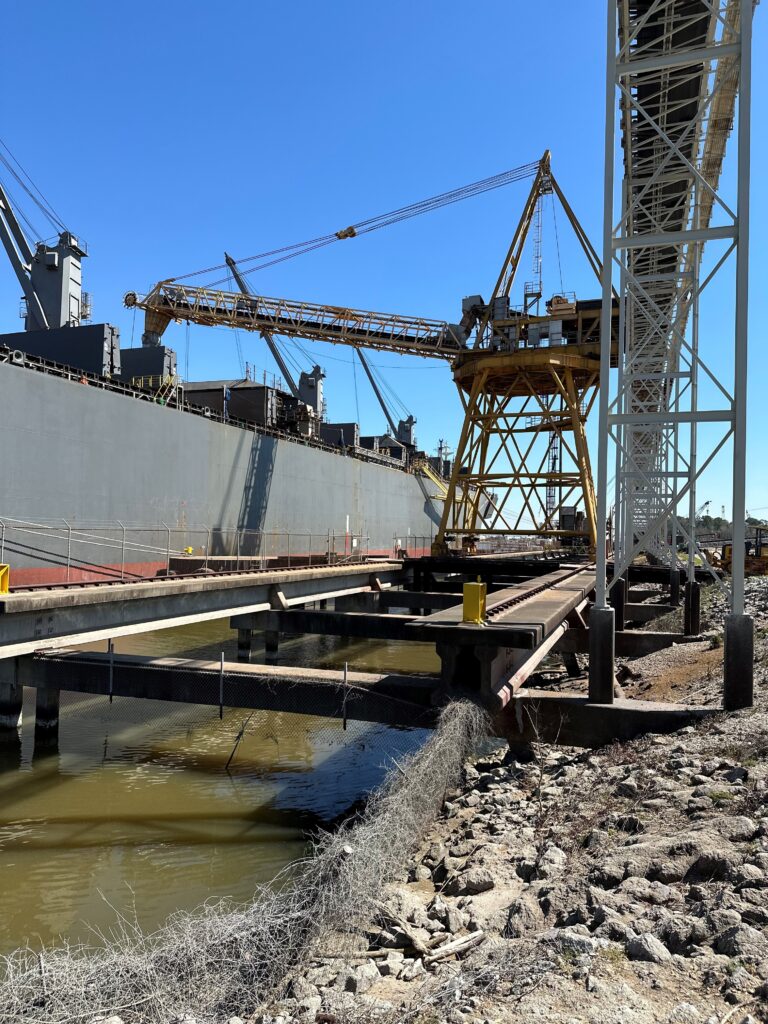
On February 24, 2024, Core Industries loaded 42,789 MT of woodchips onto the M/V YILDIZLAR 3. Core used its two Wagner Woodchip Carrydozers to feed the woodchips to the reclaim system. From there, conveyors transported the woodchips to the ship loader which utilizes a Jet Slinger to increase the rate of compaction. Core operates one […]
Loading Woodchips
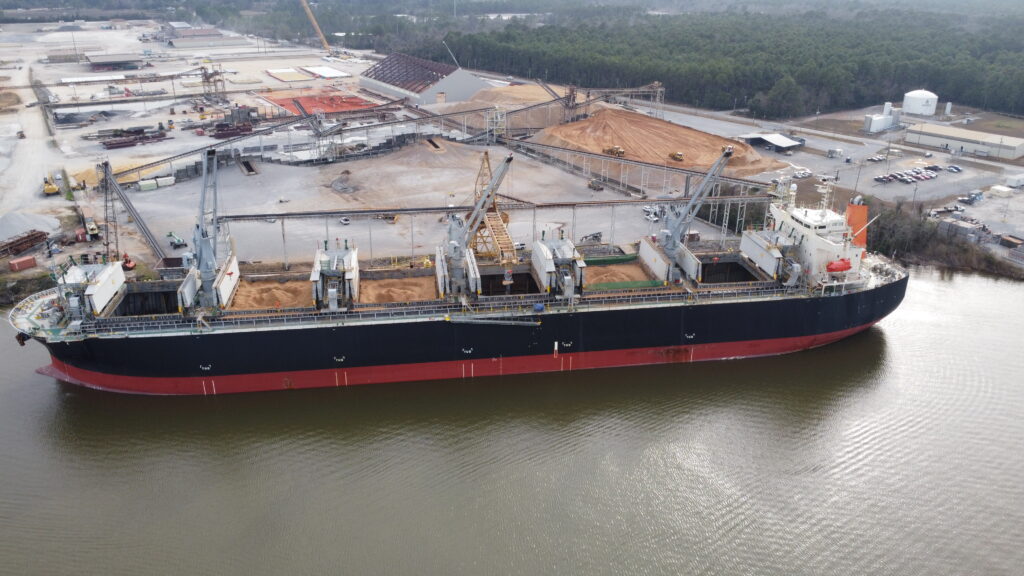
In February 2024, Core Industries loaded 43,874 MT of woodchips onto the M/V WATER LILY. Arriving by truck, the chips were stored and transported to Turkey. Core used its two Wagner Woodchip Carrydozers to feed the woodchips to the reclaim system. From there, conveyors transported the woodchips to the ship loader which utilizes a Jet […]
Loading Boats — M/V HAPPY DRAGON
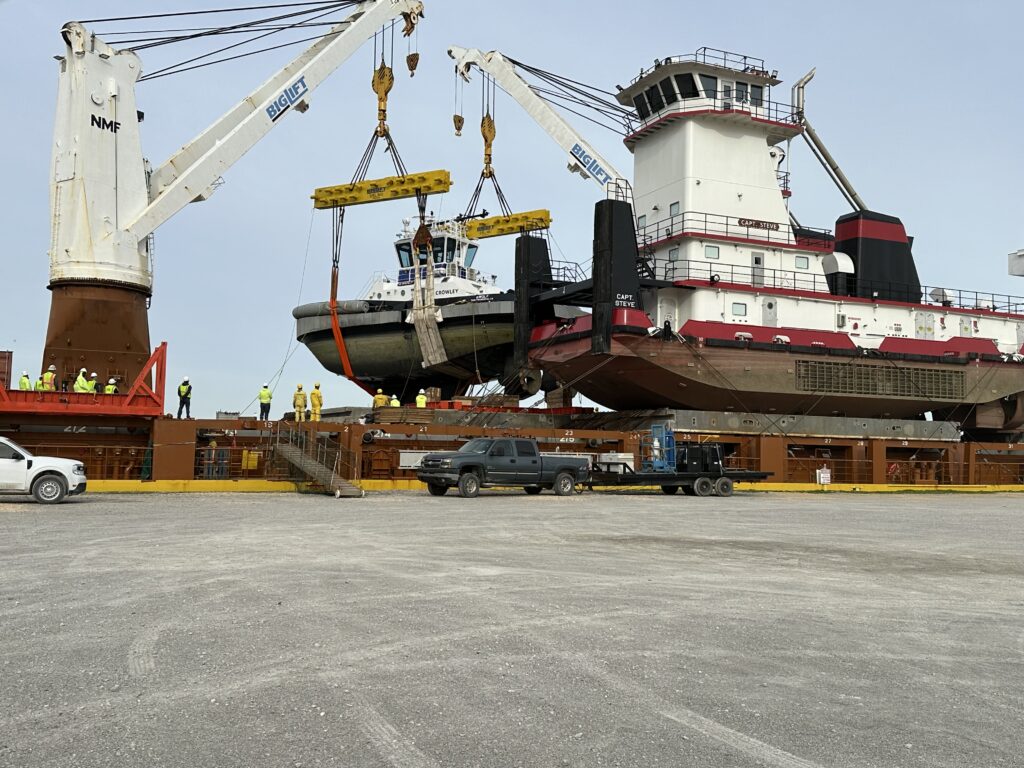
Core assisted in loading a pleasure boat and two tug boats to the M/V HAPPY DRAGON. Arriving at the Core dock under their own power, the three boats were lifted from water to vessel using the ship cranes. Core provided the dock, and Core personnel provided rigging services. Core’s staff is highly experienced in planning […]
Offloading Limestone
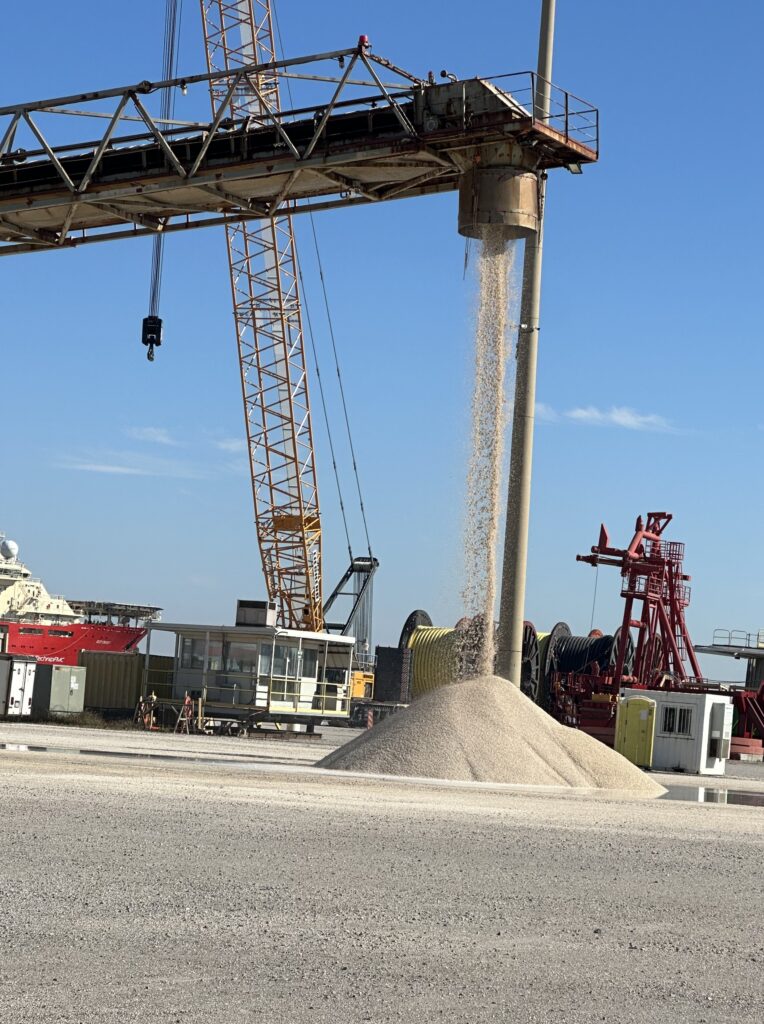
The M/V BAHAMA SPIRIT recently discharged 7,260 MT of Limestone at the Core Industries dock. Arriving from Freeport, Bahamas, the Limestone was transported to Core Calcium for processing. Core Industries used its front-end loaders to complete the job.